

Meltpool: Concept Laser showed how its Meltpool monitoring system can be used to develop 2D and 3D plots that can be superimposed with the 3D CAD file to identify problematic areas – the video is also on YouTube and embedded below.Live video: simple but useful, this allows users to get a live video stream of the top layer as it is being built and can help detection of recoater blade damage and part interaction.Oxygen Level: Sensors in the build chamber as well as in sieving stations track O2 levels to ensure the flushing of air with inert Argon or Nitrogen has been effective and that there are no leaks in the system.Laser: Sensors monitor laser powder as well as temperature across the different critical components in the system.Metal AM suppliers themselves have developed a range of in-situ monitors that were discussed in a few presentations during AMUG, and they generally fall into the following categories: Third party companies like Sigma Labs and Stratonics have developed platform-independent solutions that can be integrated with most metal AM systems. Most customers of AM machines that wish to use it for functional part production bemoan the lack of controls during manufacturing that allow them to assess the quality of a part and screen for excursionary behavior without requiring expensive post-processing inspection. This was not my intent, so I believe it is an accurate indication of what suppliers are prioritizing at this stage of the technology’s growth and see as providing key levers for differentiation. For the purposes of this post, I have picked the top-of-the-line machine that each supplier offers as an indication of the technology’s capabilities: they span a range of price points, so once again this is not meant to be a comparison.Īs a point of observation, the 5 key trends I noticed turned out to be all really aspects of taking the technology from short run builds towards continuous production. While it is interesting to study how 5 different suppliers interpret the same technology and develop machines around it, it is not my objective to compare them here, but to extract common trends that most suppliers seem to be working on to push their machines to the next level.
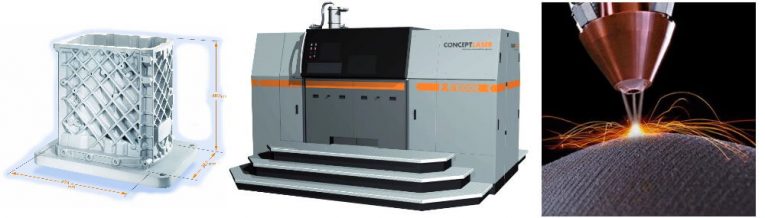
In this post, I focus on the former and try to distill the trends I noticed across the laser-based metal AM system manufacturers that were present at the conference: Concept Laser, SLM, Renishaw, EOS and 3D Systems (listed here in the decreasing order of the time I spent at each supplier’s booth). So I decided to focus on two themes: laser-based metal additive manufacturing (AM) and design & simulation for AM. One of the more difficult things about being at the Additive Manufacturing Users Group (AMUG) is dealing with the fact that there is more to do than you can hope to accomplish in four and a half days. The X Line 2000R appeals to any manufacturer who wants to produce aluminum and titanium parts with large and complex geometries.Figure 1. The system is also offered with the option of a second production module in order to minimize the idle time in the production, part loading and unloading stages.

X Line 2000R, which can operate between 30-150 µm layer thickness, has been specially developed for large-sized parts to be produced from reactive powder materials such as aluminum and titanium alloys.Įquipped with sensor and measurement technology in accordance with Explosion and Fire regulations (ATEX Zone 22 category II 2 D), X Line 2000R has a high level of safety. X Line 2000R, which has a 800 x 400 x 500mm production platform, is equipped with 2 x 1000W fiber lasers. X Line 2000R is the device with the largest production platform among 3D metal printers in the world. Meet the largest member of the LaserCUSING® family.
